1. Luminous ceramic
Luminous ceramic is a product obtained by melting high-tech luminous pigments into traditional ceramic glaze and firing at high temperature. It can absorb a variety of natural light (sunlight/other scattered light), activate the absorbed light energy, and automatically glow when placed in a dark environment. In general, luminescent ceramic is a new type of ceramic product with self-illumination function by adding long afterglow light storage material in the production process of ordinary ceramic.
Luminescent ceramics have excellent mechanical strength, wear resistance, water resistance, weather resistance, light storage and luminous properties, and do not contain any radioactive elements, non-toxic and harmless to human body, green and environmental protection; Absorbed and stored light energy can be used for life, and the enhanced luminous duration can be more than 15 hours, and the luminous performance can be repeated to maintain the luminous performance for a long time.
2. Synthesis method of luminescent ceramics
There are three main methods to synthesize luminescent ceramics:
① The powder of the luminescent material is directly fired into the luminescent ceramic block, and then processed into various shapes of finished products. The new generation of aluminate and silicate long-afterglow luminescent material itself is a functional ceramic. ② Evenly mix the luminescent materials with the traditional ceramic raw materials, and directly fire the finished luminescent ceramics. ③ Firstly, the luminous ceramic glaze is fired, and the luminous ceramic glaze is applied to the surface of the ceramic body, and the surface luminous ceramic products are fired.
3. Types of luminescent ceramics
According to different firing temperatures of luminous ceramic glaze, it can be divided into three categories:
① Low-temperature lead-containing ceramic luminous glaze: the firing temperature of this glaze is between 700 and 820 ℃. The products fired with this glaze have the advantages of high refractive index and good gloss, and the expansion coefficient of the glaze is small, which can be well integrated with the body.
② Medium-temperature luminescent ceramic glaze: the firing temperature of this glaze is 980~1050 ℃, and the firing methods are various, which can be sprayed, screen printed and hand-painted, can be made into the bottom glaze, and can be made into the third-degree fired product with the glaze particles. Medium-temperature ceramic luminous glaze is mainly used in building ceramics. It is made into ceramic products for indoor use, such as night indication, fire prevention and safety signs. It has the advantages of flame retardance and aging resistance.
③ High-temperature ceramic luminous glaze: the firing temperature of this kind of glaze is about 1200 ℃, which is similar to the firing temperature of daily ceramics and high-grade architectural ceramics. The finished products have high luminous intensity and long afterglow time.
4. Technological process of luminescent ceramics
Preparation process flow: the luminous glaze is mixed and mixed according to the set proportion, and then coated on the ceramic body or ceramic glaze by spraying glaze, casting glaze, screen printing, manual painting, stacking glaze and other processes, and then a layer of transparent glaze can be applied on the glaze surface as required. After drying, it is fired according to the different formula of the basic glaze to obtain the light-storing luminous ceramic products.
5. Use method of luminous ceramic glaze
① Mix the luminous ceramic glaze and printing oil in a ratio of 1: (0.5~0.6) and stir evenly. Use 100~120 mesh screen to print on the unburned surface glaze, and then dry it and burn it in the roller kiln of rapid firing process, with the firing time of 40~90 min. ② Mix the luminous ceramic glaze and printing oil at the ratio of 1:0.4, stir them evenly to make them thick, print them on the glazed tile with 40-60 mesh screen, and then overprint the ceramic pigment after thoroughly drying, and finally print the glaze dry powder with 30-40 mesh screen. After drying, it is fired in a roller kiln with rapid firing process, and the firing time is 40~90 min, which is the integral luminous product. ③ After mixing the luminous ceramic glaze with water evenly, evenly spray it on the white glazed tile or green body, and then apply a thin layer of transparent glaze on it. After drying, it is fired in a roller kiln with rapid firing process. The firing time is 40~90 minutes, which is the overall luminous product. ④ Mix the luminous ceramic glaze with ink or water and stir evenly. It is painted on the surface of the product by hand, dried thoroughly, and then fired in a roller kiln with rapid firing process. The firing time is 40~90 min. ⑤ The luminous ceramic paper is made of luminous ceramic glaze, and the luminous ceramic is produced by the transfer of the paper.
6. Market application of luminescent ceramics
The unique performance of luminous ceramic can prevent it from being applied to all kinds of low-intensity lighting, decorative lighting and various nameplates at night. For example, low-brightness lighting at night for families and hospital wards, building corridors, room nameplates, cinema seat plates, safety doors, electrical lighting and darkroom lighting power supply, luminous slippers, luminous telephone handles, etc.
Luminous ceramics can also be used in various decorative designs of buildings due to their ceramic properties, such as luminous gypsum ceiling, ceiling, neon decoration, decorative painting, luminous ceramic tiles, etc. Luminous ceramics can also be used to produce exquisite luminous ceramic polyester handicrafts, luminous pearls, luminous sculptures, large strokes, indicators and pointers of various clocks, instruments and meters.
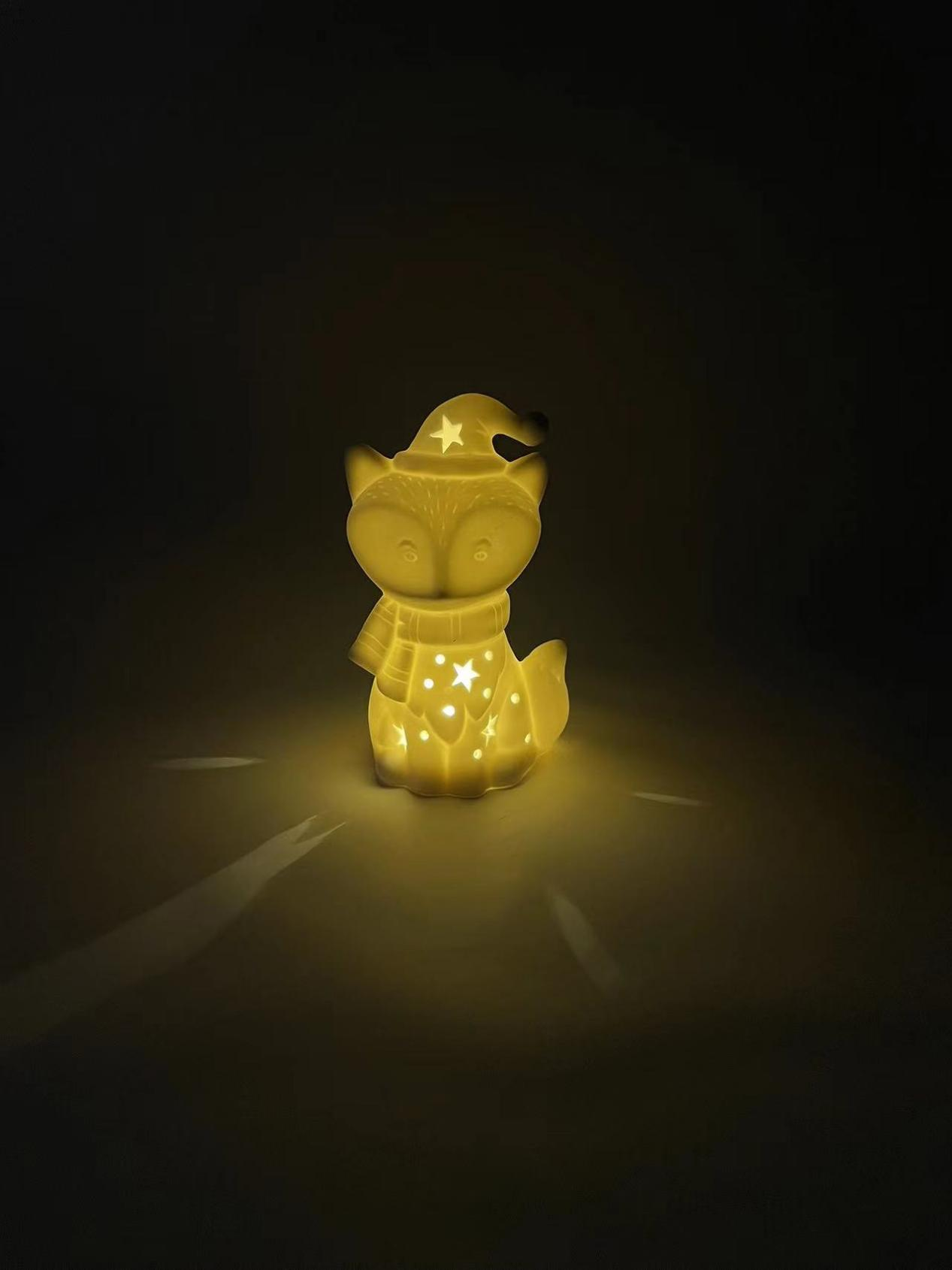