The ceramic production process can be divided into four stages: raw material production (glaze and clay production), molding, glazing and firing.
Raw material production is divided into:
1. Glaze production
Glaze → ball mill fine crushing (ball mill) → iron removal (iron remover) → screening (vibrating screen) → finished glaze
2. Mud production
Mud material → ball mill fine crushing (ball mill) → mixing (mixer) → iron removal (iron remover) → screening (vibrating screen) → slurry pumping (mud pump) → mud squeezing (filter press) → vacuum mud refining (mud refiner, mixer)
Forming is divided into: blank forming method, clay plate forming method, clay bar plate forming method, freehand kneading method, and manual sculpture forming.
The drying of ceramics is one of the most important processes in the production process of ceramics. Most of the quality defects of ceramic products are caused by improper drying. Fast drying speed, energy saving, high quality and pollution-free are the basic requirements for drying technology in the new century.
The drying of ceramic industry has gone through natural drying, chamber drying, and now the continuous dryer with various heat sources, far infrared dryer, solar dryer and microwave drying technology.
Drying is a relatively simple but widely used industrial process, which not only affects the quality and yield of ceramic products, but also affects the overall energy consumption of ceramic enterprises.
According to statistics, the energy consumption in the drying process accounts for 15% of the total industrial fuel consumption, while in the ceramic industry, the proportion of energy consumption used for drying in the total fuel consumption is far more than that, so the energy saving in the drying process is a major issue related to the energy saving of enterprises.
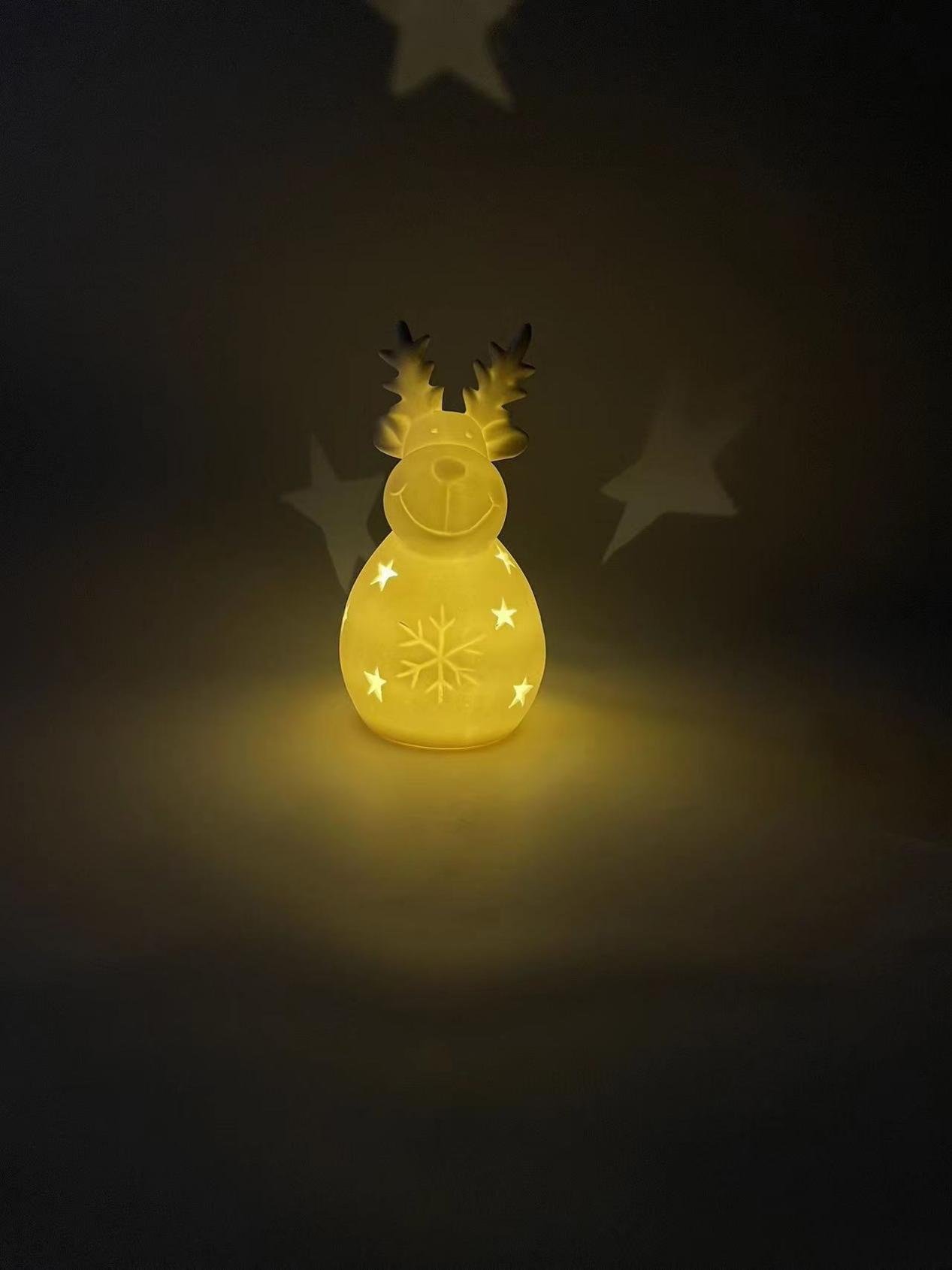